Six months ago I sat in on a conference, listening to Dr. Michael Harvey introduce a new funding scheme available to early career researchers (ECRs). The scheme was FLEET’s Translation Program – designed to encourage ECRs to take on projects that expanded their field, generate impact, and translate their research to industry applications. As a PhD candidate in condensed matter physics, I was already exploring a concept to simplify some time-consuming processes in my research. His talk was the nudge I needed to push this idea forward.
Working with Scanning Tunnelling Microscopes (STMs) is a large part of what I do and although they’re incredibly powerful tools – capable of characterising surfaces with atomic-scale resolution – the quality of the data they produce is only as good as the scanning probe used to acquire it. One persistent challenge is the slow routine of data acquisition and the frustrating need to constantly refine the delicate apex of the probe. To address this, I’d been pondering on a concept I called Scanbot – a Python-based robot designed to automate these tasks.
The thought of automating these routine tasks was exciting, and with encouragement from Michael, I submitted my proposal. Receiving approval for the project was a significant milestone; it was an acknowledgement of the potential impact of Scanbot, and it spurred me on to the development phase.
Building Scanbot was a process full of challenges and learning. The robot needed to identify when the STM tip required refining, carefully navigate to and from a reference metal (ideal for refining the probe) and a sample of interest, as well as autonomously image the sample surface. Each of these steps presented its own hurdles.
Developing an algorithm for bad tip detection was the first task. After much coding, testing, and refining, Scanbot was capable of distinguishing a poorly shaped tip based on the acquired images. Admittedly, there’s still room for improvement here but for a proof of concept, I had more than enough.
Next was the creation of a navigation system. Using a camera feed to monitor the tip’s position above a dual sample holder, Scanbot was programmed with the ability to control the STM motors and guide the tip precisely to a clean reference metal and back to the sample.
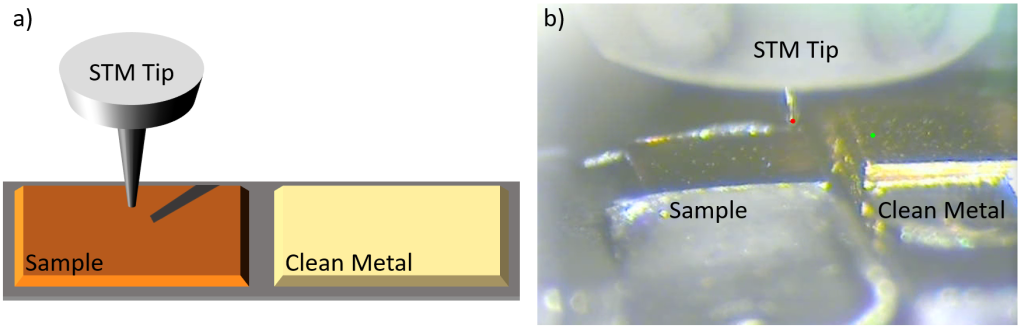
Finally, the refining process required Scanbot to be able reshape the STM tip by carefully poking it into the clean surface and analysing the crater left behind. This is an iterative process which is repeated until the desired tip geometry is achieved.
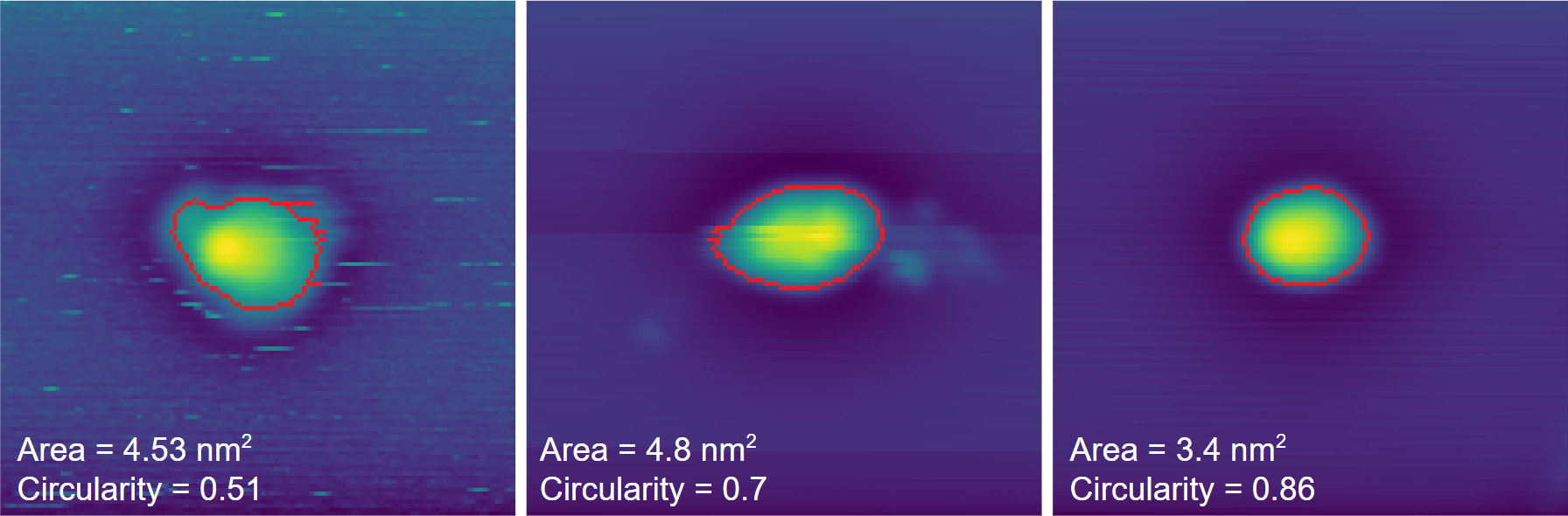
Seeing Scanbot successfully complete its first cycle was a milestone. It marked the transition from an abstract concept to a functional tool, demonstrating how automation could simplify STM research. Currently, Scanbot is open source and accessible on GitHub, ready to be utilised and further developed by the wider scientific community. The journey from hearing about the FLEET Translation Program to making Scanbot a reality has been an enriching experience. It’s made me appreciate the role of automation in research and has shown the potential impact of initiatives like FLEET that support original ideas. As Scanbot continues to evolve, I’m excited to see how it will contribute to STM research.
Before I leave you with the below survey, autonomously acquired by Scanbot, I would like to acknowledge contributions to the Scanbot project from Jack Hellerstedt, Benjamin Lowe, and my PhD supervisor, Agustin Schiffrin.
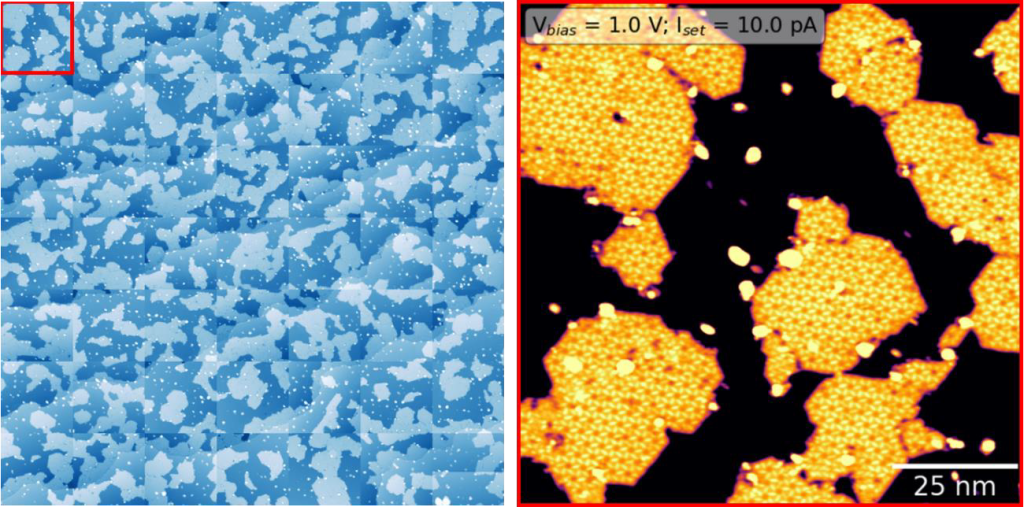